OPINION: The Airline Industry’s Need for Network Resiliency
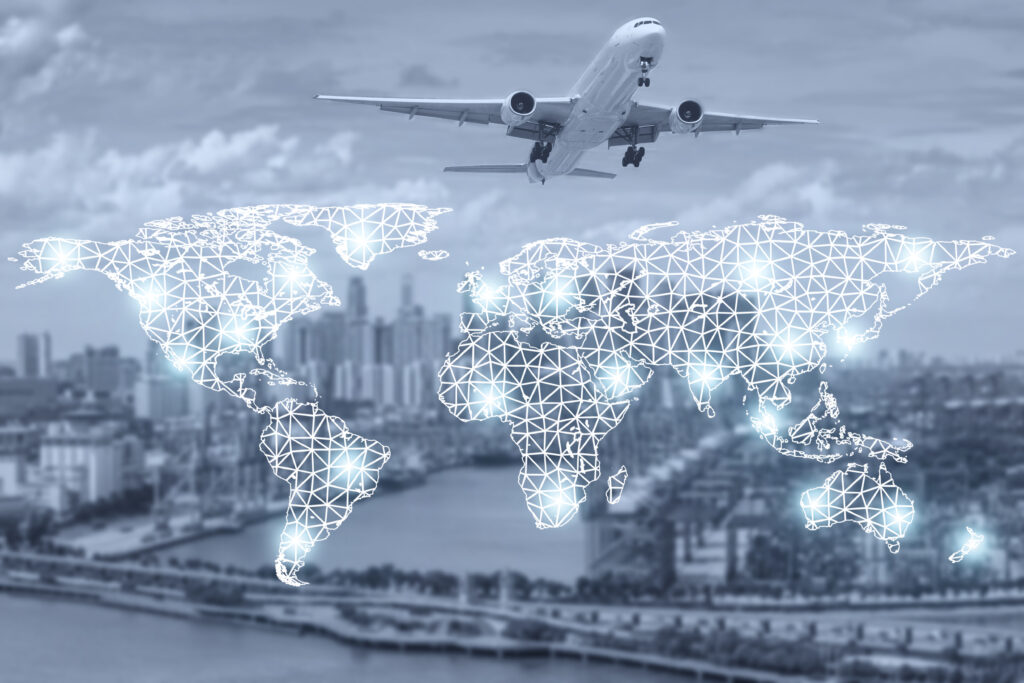
The Airline Industry’s Need for Network Resiliency Amid Digitalization (Photo: ICAO/NASA)
The airline industry, a cornerstone of the global economy and supply chain, continues to invest heavily in digital initiatives to optimize outdated processes, boost productivity, and open new revenue streams. According to Frost & Sullivan’s analysis of the global airline digitalization market, big-name airlines, particularly those in Asia-Pacific and North America, are keen on migrating most of their IT infrastructure to the cloud within the next decade.
With the market estimated to reach $35.42 billion by 2030, airlines are eagerly pursuing digitalization, implementing next-generation technologies like the Internet of Things (IoT) sensors and cameras, Big Data, and advanced data analytics.
Air cargo is an archetypical example of this shift toward digitalization. Currently, air cargo represents a considerable chunk of airlines’ bottom lines, and as it grows, the supply chain must become more connected and digitalized. To achieve such a supply chain, airlines and international trade organizations are cooperating to deploy new technologies that streamline operations and enhance visibility through improved data sharing and availability.
These new technologies and initiatives include One Record, interactive cargo, and Cargo Connect. One Record, a common data model shared through standardized and secured web API, enables supply chain managers to view shipments through single records. Airlines also use interactive cargo to create responsive air cargo services, permitting them to self-monitor, send real-time alters and track cargo locations. Cargo Connect simplifies communications between distributors, freight forwarders, and airlines.
While undeniably valuable, all these technologies and initiatives essential to supply chain visibility depend on a secure, always-on and connected network. In fact, the greater reliance airlines place on these complex digital systems and solutions, the more vulnerable they become to sudden disruptions. In an industry where time is everything, the consequences of prolonged inaccessibility to critical platforms and infrastructure could be disastrous, monetarily and from a reputation perspective.
Southwest Airlines recently experienced a days-long collapse of its entire system at the peak of travel season. Although the cause of Southwest’s outage was due to a corrupted database file in a pilot’s advisory system, many other variables can cause network disruptions, such as ISP carrier issues, human error, and data breaches.
Network outages can also spawn from software updates and patches, which is particularly concerning today due to the push for digitalization. The infrastructure of most airlines cannot meet modern requirements for digital transformation, which hints at the ongoing efforts to replace and update legacy hardware and software. As a result, airlines need a resilient network to recover quickly from the inevitable outages arising from these technology overhauls and integrations.
Additionally, network engineers rely on Transportation Management Systems (TMS) to uphold security, compliance, and performance requirements. A TMS enables supply chain operators to manage all transportation activities through standardized processes. Nevertheless, without an independent management plane, any network outage, whether from a software update or a human mistake, will prevent engineers and operators from accessing their TMS, grinding operations to an unceremonious halt.
For all these reasons, airlines need a secure and reliable means of accessing their critical infrastructure to ensure business continuity, especially during disruptions. One approach to achieving such a posture is through a Smart Out of Band network. This type of network empowers airlines to separate and containerize functions outside of the management plane, creating an independent management plane that operates freely from the primary in-band network.
Similarly, network engineers can leverage a Smart Out of Band network to securely and remotely access and manage infrastructure and resources, allowing them to safely identify and remediate network issues without interfering with operations. Moreover, by combining a Smart Out of Band network with a Failover to Cellular solution, airlines can preserve the visibility of their entire network during outages.
Of course, ensuring emergency access to critical resources when the primary network goes down is not the only responsibility of a network engineer—especially during digitalization. There is also first-day provisioning as well as day-to-day configuration. As such, airlines should, amid their ongoing digital transportation efforts, prioritize those network resilience solutions that support and enhance the everyday management and monitoring of IT infrastructure.
This article is authored by Tracy Collins, Opengear’s VP of Sales, Americas.
Tracy has over 25 years of experience in leadership positions in the IT and infrastructure industry. Prior to joining Opengear, Tracy led the Americas business for EkkoSense, the leading provider of AI/ML software that allows data center operators to operate more efficiently. Prior to joining EkkoSense, Tracy was the CEO of Alabama-based Simple Helix, a regional colocation data center operator and MSP. Tracy spent over 21 years with Vertiv in various leadership positions including leading the global channel organization.
—————
Boost Internet Speed–
Free Business Hosting–
Free Email Account–
Dropcatch–
Free Secure Email–
Secure Email–
Cheap VOIP Calls–
Free Hosting–
Boost Inflight Wifi–
Premium Domains–
Free Domains